倍耐力是世界上唯一一家在意大利工业化生产自行车轮胎的企业。在米兰郊外的Bollate工厂,生产公路、砾石和山地自行车领域顶级规格的轮胎,这些产品目前是倍耐力供应的核心。这些产品在高度自动化的生产线上生产,不仅确保了其品质卓越,也确保了高质量的工作场所及环境。
从这一角度来看,倍耐力处于时代前沿:上世纪 80 年代末,随着世界上首批全自动轮胎生产厂之一(汽车轮胎)的落成,公司开始积累高科技生产线的经验。基于时间与经验的积累, Bollate自行车部门设立,并在此使用了最新的自行车轮胎生产线,该生产线由倍耐力负责设计和生产机械的部门临时创建。在 2019 年伊始的复杂工业转型结束后,于 2022 年正式投入使用。
为什么高度自动化可以确保轮胎质量?为了了解这一点,让我们先来探究该产品的诞生过程。
初生稚嫩,终至坚韧
众所周知,轮胎非常坚固耐用,根据不同的产品类型,可以装配从卡车到自行车的任何车型。然而,在硫化之前的过程中,其半成品部件非常脆弱,以至于仅仅处理它们就有可能将其损坏。为了强调这一概念,可以说最好的生产工艺就是无菌工艺:最好避免人工接触,尽可能实现自动化操作,从部件、纺织品、化合物、强化部件等,Bollate工厂正是为此而设计的。
此外,高度先进的自动化工艺确保了成品的精度最大化,这对每条轮胎,尤其是轻型和超轻型自行车轮胎而言至关重要。
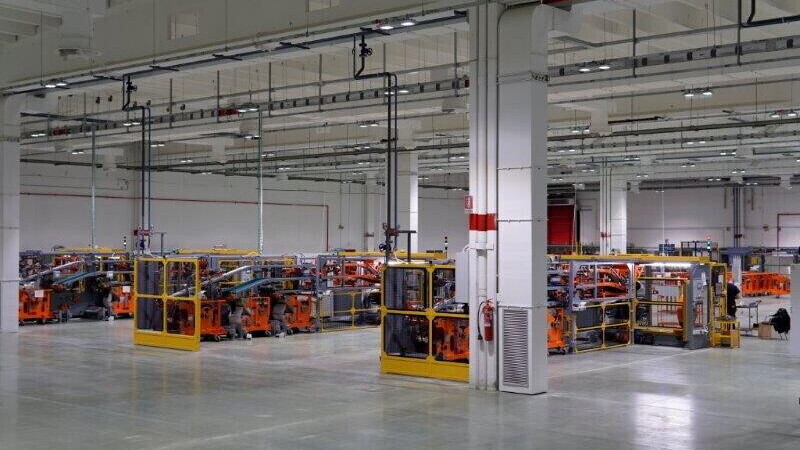
生产周期
Bollate工厂的生产线由一条中央通道组成,产品在此组装。这里是成品轮胎的诞生地,包括所有部件,然后进入硫化阶段。走廊的两侧是半成品区,机器分为两组:一组是纺织部件的准备区,另一组是胎面的准备区。
目前有不同的装配点,用于三条产品线(公路、砾石和山地自行车)。
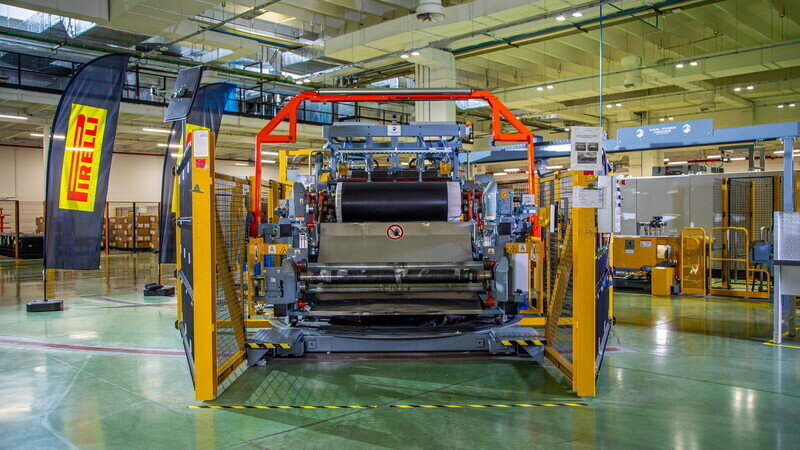
胎体结构
胎体的基本要素是织物带和配方的质量,倍耐力凭借在生产高性能轮胎方面获得的丰富经验,在这两个方面均造诣颇深。
要制作胎体,需要使用非常薄的橡胶织物(十分之几毫米),再加上聚酰胺花纹,最后使用芳纶纤维饰边,这是一种先进的技术材料。这些纤维在到达工厂时被包裹成螺栓状,然后通过切割机切割成适合轮胎类型的宽度,因此,从最薄的公路轮胎到最宽的山地自行车轮胎,都有相应的纤维带。
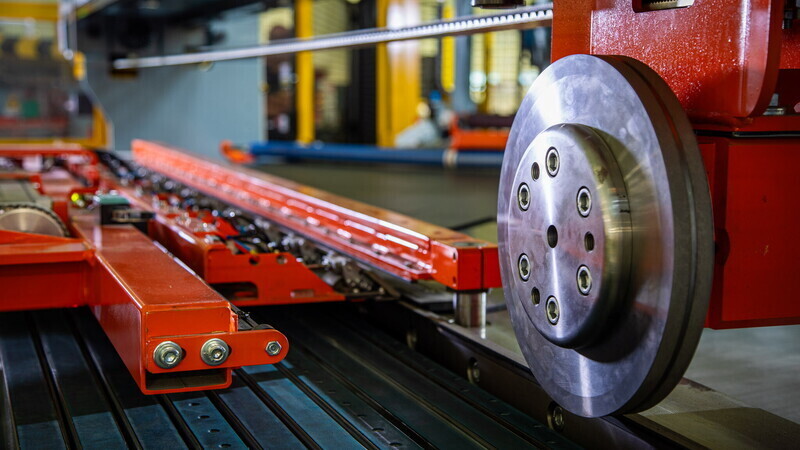
胎面
胎面花纹带的核心是配方,这是倍耐力的优势,它以管状形式运往罗马尼亚的Slatina工厂或Settimo Torinese工厂。胎面花纹带由此产生,对于公路轮胎而言,胎面花纹带呈非常薄的半月形。胎面花纹带非常重要,因为它紧贴地面,决定了轮胎的性能:平顺性、抓地力和磨损性。
首先是由倍耐力设计的模具进行挤压成型的工序:一个料斗将配方加工成所需的胎面花纹带类型。在这一过程的下游是检查仪器,对参数(温度、宽度、厚度)进行检验,随后经过冷却通道。该设备还能生产双复合胎面花纹带。
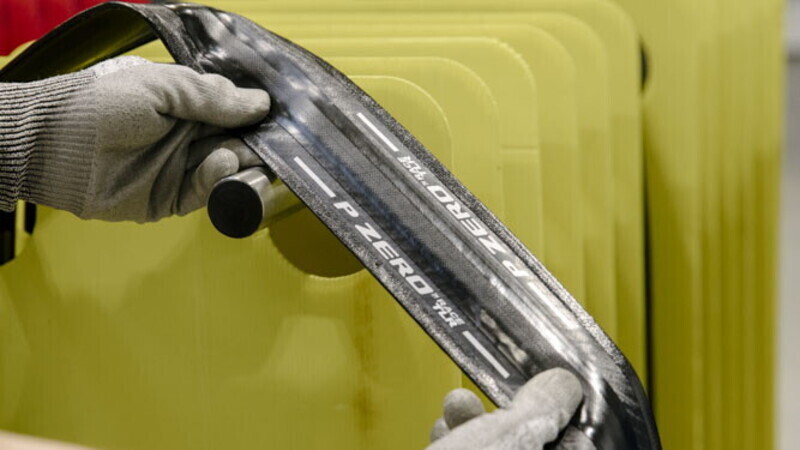
组装
组装机由一个滚筒组成,轮胎的所有部件都围绕滚筒延展。组装过程从胎体结构开始,最后在胎体上添加胎面花纹带。根据组装的轮胎型号,还可预见其他组件,如不同类型的加固层、防刺穿层、无内胎轮胎(TLR)的防水层。
整个过程自动化且安全,操作人员无需靠近生产设备。
此时,轮胎生产的各个环节都已完成,但由于尚未进行硫化,所以其仍处于较脆弱的状态。要理解硫化这一概念,可以将其视为一种部件的整合处理,其旨在强化胎体并使胶料具备更强的耐磨性。
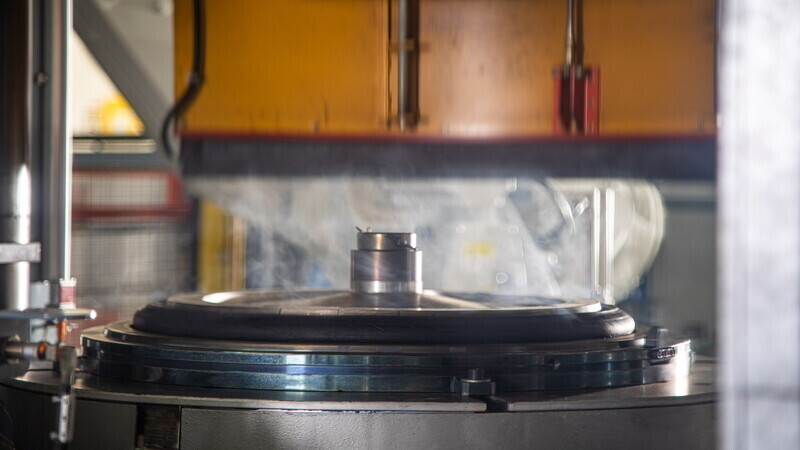
硫化:最后一道工序
硫化将化合物从塑性状态转变为弹性状态,使轮胎均匀、易于管理并可安装到自行车上。实现这一过程的方法是将生胎预先放置在硫化机的处理装置上:整个操作过程完全自动化。根据轮胎类型、温度、压力和/或时间的不同,整个周期只需几分钟。之后,成品将自动送往质量控制部门。
由于硫化机会产生热量和烟雾,因此必须从环境角度对其进行监控,为此,硫化机被封闭在一个装有吸气装置的舱室内,该系统有三个优点:可以保持操作条件的稳定,这对保证产品质量非常重要;由于舱室外的温度受到控制,因此可以确保为工人提供一个舒适的环境;通过限制热量的扩散,有利于节约能源。
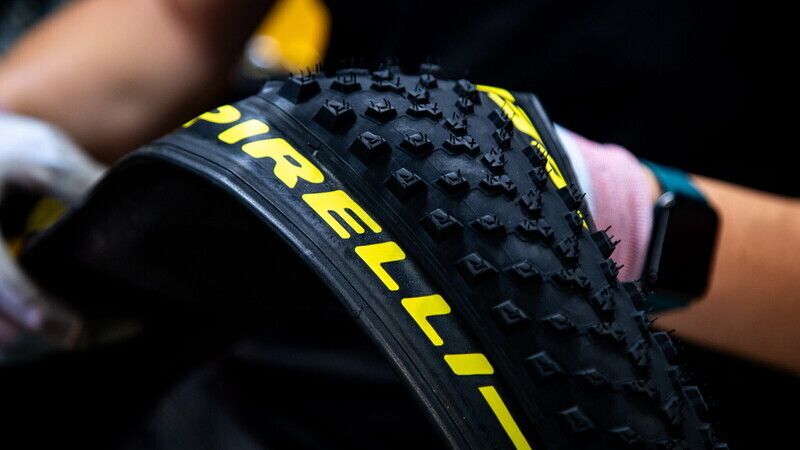
质量控制
每条轮胎都要经过质量控制部门的层层检验。这一过程由工人手工完成,他们对成品的每个细节进行检验,并检查瑕疵。